In recent years, we have seen how Lidar technology has conquered the market in an extraordinary way. The reliability of the capture, the accuracy and the speed of acquisition are factors that have been decisive in the diffusion of this technology. Furthermore, in the last 10 years [ref 1], thanks to technological progress, it has been possible to produce portable Lidar Scanners. This has resulted in a moderate loss of precision, but has increased the dynamism and acquisition speed, making these instruments suitable for different types of applications.
Photogrammetry and computer vision in the field of image-based sensing have also evolved impressively in recent years. It is now possible to compute homologous points from hundreds of images with remarkable reliability and flexibility. The processes are now much faster and more accurate, thanks also to the improvement of the internal orientation techniques, and the textures have a higher resolution with better balance.
This scenario allowed the development of a new scanner: Stonex XVS vSLAM 3D Scanner; a new instrument category, incorporating a real-time image-based 3D scanning system. XVS uses two cameras: the first one for the simultaneous localisation of the equipment in real time (Visual SLAM) and the other one captures high-resolution and high-quality images. The scanner is connected via cable to a tablet equipped with a software capable of guiding the user during the acquisition, providing all the information regarding the collected data and the trajectory in real time.
The user walks and scans in a simple and intuitive way, moving freely in the space. This simplicity of use allows you to carry out very long scans without getting tired and without losing any data (we have made acquisitions of more than an hour). This does not mean that it is not possible to acquire different scans which can then be automatically merged later to increase user comfort.
CAMERAS & VISUAL SLAM
XVS consists of two cameras and an inertial measurement system (IMU). The first camera, used for Visual SLAM together with the guidance system, enables an essential function: it is the guarantee that the acquisition in the field is performed in such a way that the processed data is of high quality. This method of data collection allows you to be sure that the models will always be connected and that there will be no errors during processing.
This is a very important factor, since classical photogrammetry, and most image-based sensors, cannot guarantee the same quality combined with the ease and speed of acquisition. With other tools, there is always the uncertainty of having collected accurate data and the risk of having to go back to the site to reacquire the missing data.
The other camera has a resolution of 5 megapixels with a 2/3″ sensor and a pixel size of 3.45 microns. The sensor is a global shutter type which allows the user to move the camera without distorting the image. It is important to note that the sensors of smartphones and tablets use rolling shutter technology and may present small deformations in the image which affect the accuracy of the measurements, if you decide to collect photogrammetric data with these devices.
The inertial measurement system (IMU) is used to level the scanner and to establish the initial internal orientation values which, together with those resulting from the Visual SLAM, maximize the chances of success in 3D reconstructions with very complex trajectories.
AUTOMATIC IMAGES SELECTION
During a data collection, XVS captures hundreds of images per minute. It is understandable to think that neither the processing of all images nor the systematic selection can be acceptable solutions for data processing purposes. Therefore, during the design of the XVS scanner, an intelligent automatic image selection system was developed. This is a product of the PHD thesis of Pedro Ortiz Coder [Ref 2], which guarantees the best possible results, maximizing the accuracy and resolution of the models. It’s not about using the minimum number of images possible, but rather the optimal number of images so that the results have the best possible quality.
This automatic selection is done with care. The proprietary algorithm selects the best images based on multiple factors: object distance, user speed, image matching, image quality/field of view, etc. This increases the accuracy of the selected images.
3D SPECIFIC RECONSTRUCTION
The procedure continues with the internal orientation of the images. At this point the internal calibration of the photogrammetric camera is used, and special care is taken to maximize accuracy. The internal orientation recalculates the homologous points collected during the videogrammetric shooting in continuous capture.
CASE STUDY: BASÍLICA DEL TRAMPAL
To demonstrate the capabilities of this new videogrammetric system, a scan of the interior and exterior of the Visigothic Basilica of Santa Lucia del Trampal, in Alcuescar, Spain, was performed. This basilica originally dates to the 7th century, although it has undergone several major changes since then. It is currently the only Visigothic building in good condition located in the southern part of the Iberian Peninsula.
For this scan we used the Stonex XVS scanner and 10 points outside the basilica were collected with a GNSS-GPS. The external scan took 5 minutes and the internal scan took 9 minutes. The internal scan is started and finished on the external facade, with the aim of automatically aligning both areas. During the scan, the XVSapp software (installed on a Microsoft Surface Pro tablet) was used for data collection which allows you to manage all the parameters and have all the fundamental information in real time. The XVScloud software was used for data processing, which collects the information and sends it to a server with the parameters set by the user. Among other parameters it is possible to select the quality of the mesh, which in this case was of medium quality.
To compare the data, a scan was performed with an highly accurate terrestrial laser scanner, which was placed in 16 different positions and spheres were used to increase the precision of the registration. The result of the comparison between the scanner models (laser scanner and videogrammetric scanner) shows a minimal deviation:
The average distance between the two models is 4 mm outside (Sigma=0.07) and 10 mm inside (Sigma=0.04).
In conclusion, the videogrammetric scanner is undoubtedly a fast and accurate alternative to the static and dynamic scanners available on the market, with fantastic results in terms of texture quality. The XVS videogrammetric scanner proved to be handy, lightweight, and easy to use. Thanks to its ease of use, it is a tool that can also be used by people who are not specialized in the field of measurements.
Due to its characteristics, XVS works very well with heterogeneous textures, which is why the main fields of application include archaeology, construction, architecture, cultural heritage, urban planning, accident reconstruction and geology.
XVS proved to be an extremely easy and flexible system, but also precise and powerful. It is suitable for experts and novices alike and is able to carry out long acquisitions without issue. It can manage short acquisitions, which can be joined later without alignment problems, thanks to the characteristics of the system.
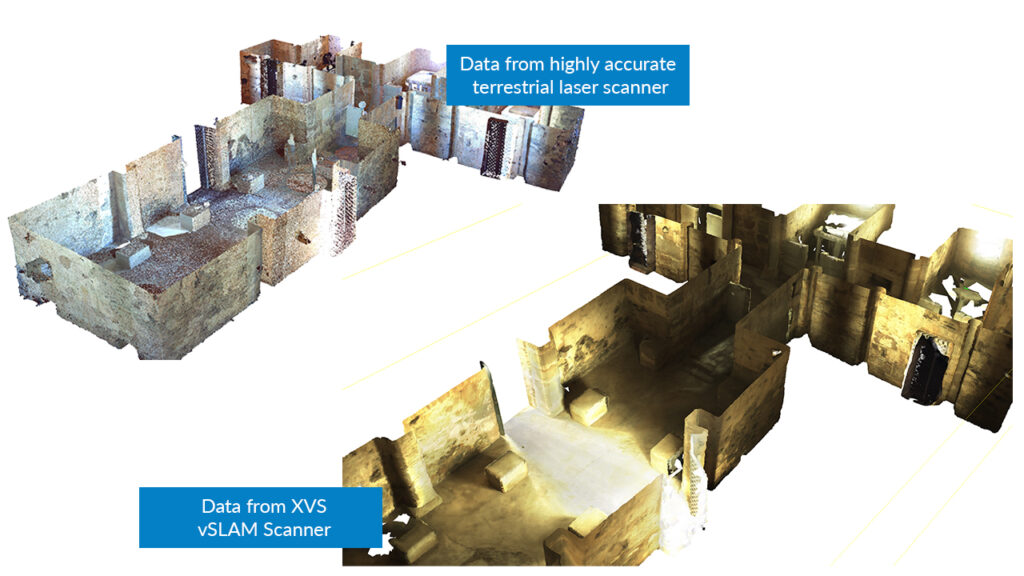
bibliography
[1]. Bosse, Michael & Zlot, Robert & Flick, Paul. (2012). Zebedee: Design of a Spring-Mounted 3-D Range Sensor with Application to Mobile Mapping. IEEE Transactions on Robotics. 28. 1104–1119. 10.1109/TRO.2012.2200990.
[2]. Pedro Ortiz Coder. Year 2021. Title: Reconstrucción 3d a través de un sistema videogramétrico basado en la utilización de visualslam y un procedimiento específico de selección de imágenes. Dehesa Repositorio. ID: http://hdl.handle.net/10662/12319